Gecdon has recently unveiled its state-of-the-art group-level FDC (Fault Detection and Classification) solution, designed to facilitate centralized data management and intelligent analysis across multiple plants and diverse equipment types. Leveraging a distributed architecture and a standardized rule engine, this solution ensures group-wide unified scheduling for equipment data collection, anomaly detection, and root cause analysis, thereby eradicating the "data silos" issue commonly encountered with traditional decentralized FDC systems.
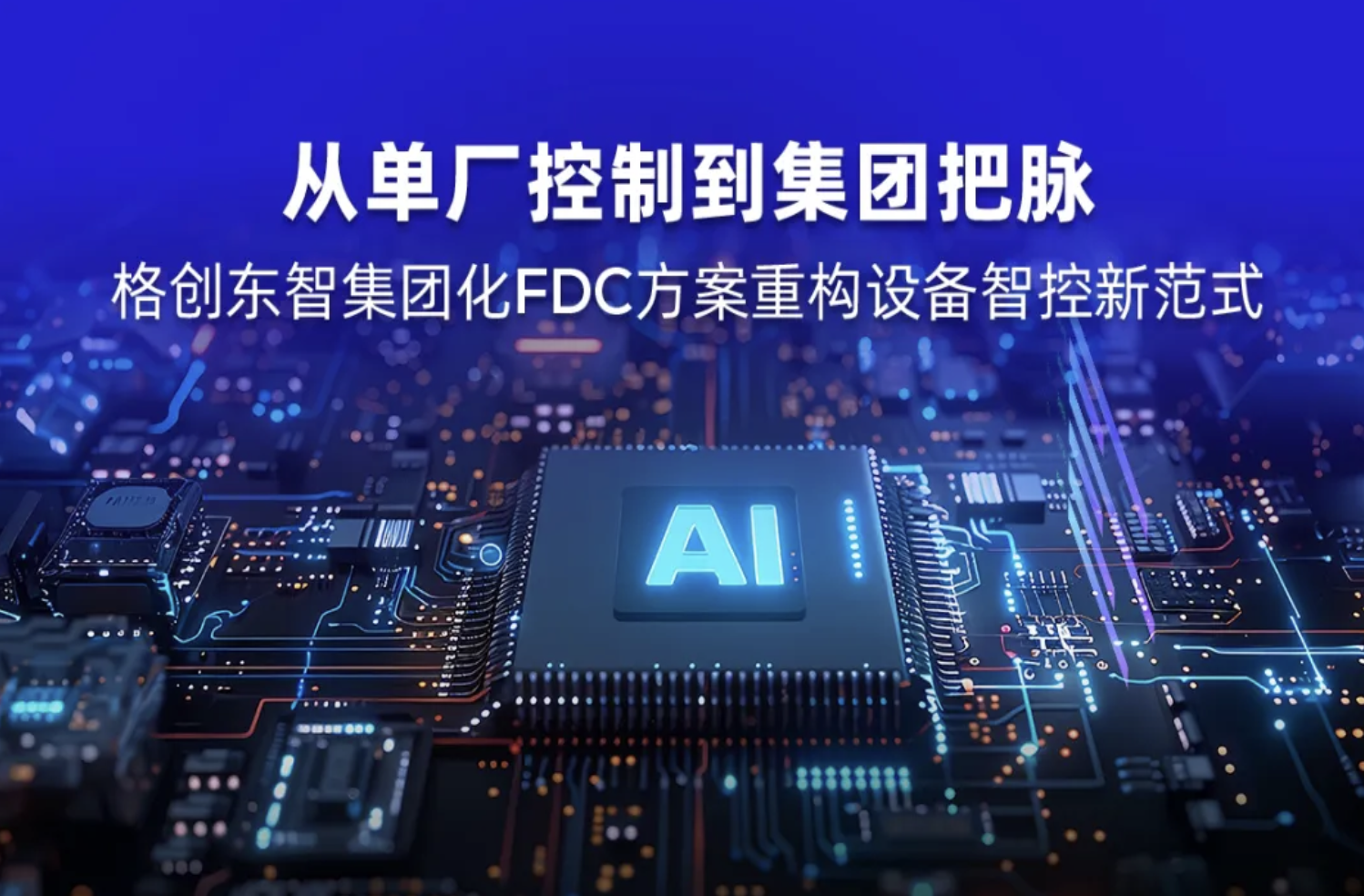
With the semiconductor industry continually evolving, leading enterprises now operate multiple fabs in a collaborative manner. However, each fab's FDC system confronts specific challenges:
Group-Level FDC Solution
Transforms cross-fab semiconductor equipment monitoring from "reactive firefighting" to "comprehensive prevention":
- Data Fragmentation Across Fabs: Traditional FDC systems fail to compare equipment parameters across fabs, hindering specification tightening and tool matching efficiency.
- Equipment Failures and False Alarms: Static rule-based systems exhibit high false alarm rates and struggle to adapt to dynamic process parameter changes.
- Inconsistent Model Configuration Standards: Lack of uniformity in FDC parameter standard configuration across fabs leads to inefficiencies in management.
- Inefficient M2M Difference Analysis: Inability to perform differential analysis on model parameters of similar equipment across fabs impacts production equipment consistency and stability.
Recognizing these challenges, Gecdon, with its profound understanding of semiconductor manufacturing scenarios and combining FDC product advantages with advanced solution-building capabilities, has developed a group-level FDC solution tailored to address the pain points of leading customers. Through its core values of group-level deployment, AI-driven differential analysis, and high compatibility, Gecdon promotes advanced manufacturing, initiating a new paradigm in intelligent equipment control.
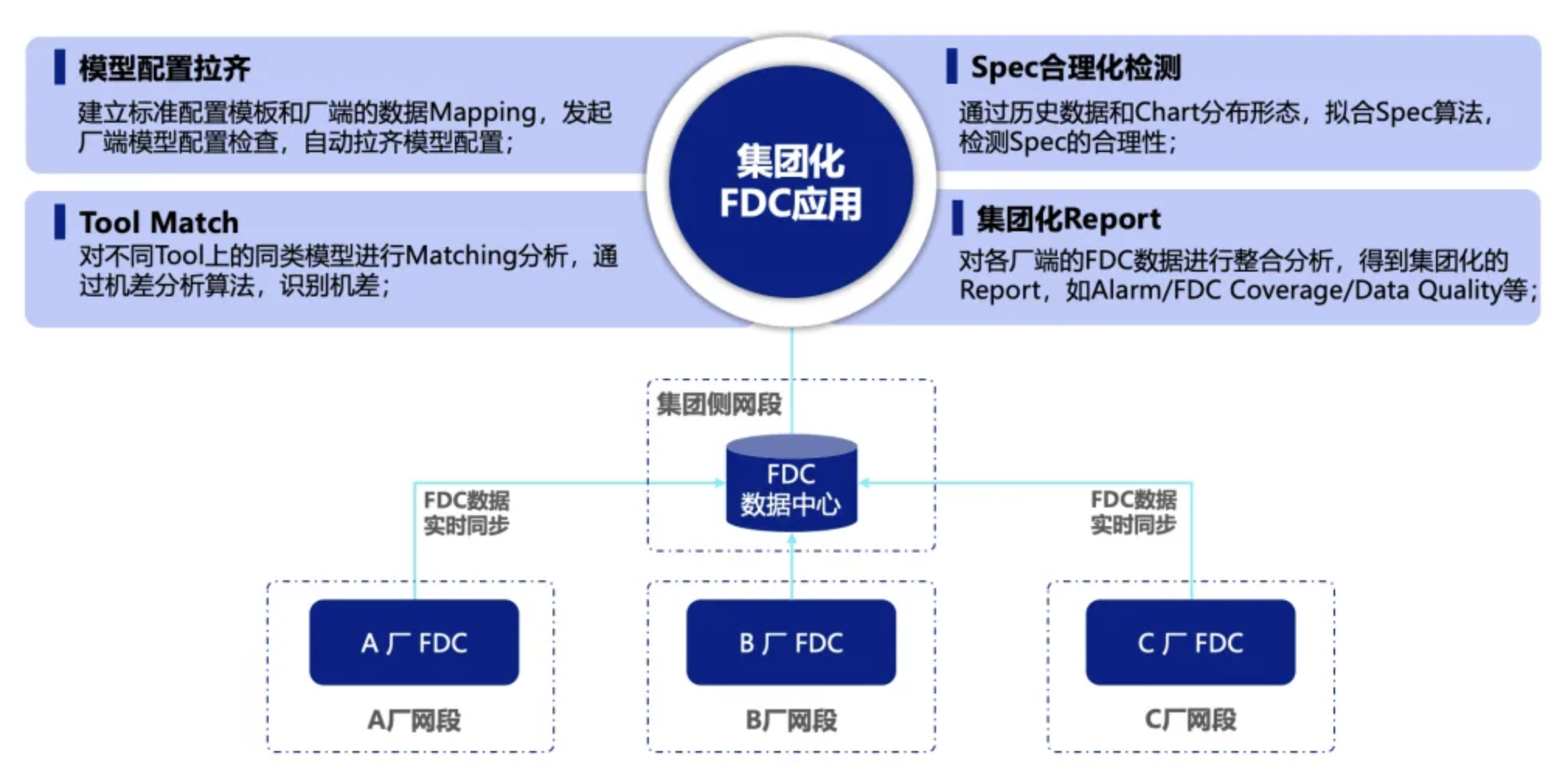
Group-Level FDC Solution
Breaks down cross-fab FDC silos, establishing a group-wide intelligent equipment control hub:
- Group-Level Deployment, Constructing a Collaborative Management System:
- Cross-Fab Data Management: Real-time synchronization of FDC data from each fab to the group FDC platform enables millisecond-level response to equipment metric anomalies.
- Standardized Configuration Alignment: Establishing mapping rules for process types, sensor naming, etc., on the group FDC platform automatically detects and corrects over 90% of non-standard configurations.
- Intelligent Specification Optimization Management: Based on historical data fitting algorithms, dynamically recommends optimal control limits, significantly enhancing anomaly detection rates while reducing invalid alarms.
- AI-Driven Differential Analysis, Accurately Preventing Hidden M2M Difference Risks:
- Differential Analysis Matching Engine: Through trend matching, distribution comparison, performance validation, and process tracing, achieves a 360° assessment of equipment status; real-time model optimization through machine learning significantly reduces false alarm rates.
- AI Decision Support: Automatically triggers early warnings and swiftly locates the root causes of M2M differences when equipment serial averages deviate.
- Seamless Compatibility with Third-Party FDC, Forming a Centralized Management Cockpit:
- 100% compatibility with third-party FDC, lossless data access, providing group-level reports.
- Integrated analysis of third-party FDC data across fabs, generating group-level reports.
- Uniformly establishes standard configuration templates, automatically checks and corrects model configurations across multiple FDC systems, improving management efficiency.
Typical Scenarios
The group-level FDC solution extends from single-plant to group-wide, enabling digital collaboration to cover the 'lifeline' of every piece of equipment:
- Multi-Fab Equipment Collaboration: Enterprises require cross-fab FDC parameter comparative analysis to achieve group-level specification standardization.
- Complex Process Optimization: In various scenarios such as front-end manufacturing, multi-factor system analysis is required to improve anomaly interception efficiency.
- Third-Party System Adaptation: Seamlessly migrates original FDC modeling data, providing localized functions such as OA approval and closed-loop management.
- Real-Time Production Assurance: Addresses invisible issues such as equipment power outages and process interruptions, achieving second-level alerts in combination with the system platform.
Industry Benefits
The 'FDC Super Brain' responds to the group-wide demand for continuous production of equipment:
- Efficiency Improvement: Forms group-level data integration and analysis, unifying cross-fab FDC models, shortening configuration synchronization time from weeks to hours, and significantly reducing labor input.
- Cost Savings: The group FDC cockpit conducts fault prediction and differential analysis based on big data analysis, reducing equipment downtime losses and significantly lowering equipment maintenance costs.
- Intelligent Upgrades: The group-level FDC system integrates AI technology, enhancing response speed and accuracy, and driving the transformation of advanced manufacturing from 'report management' to 'cognitive decision-making'.
Customer Case
During Gecdon's service for a leading 12-inch wafer fab cross-fab customer, the customer's third-party FDC systems across three fabs faced challenges such as single-point operation, poor coordination, and inability to simultaneously gain a comprehensive view of cross-fab equipment status.
Gecdon conducted an in-depth analysis of the customer's current situation and provided a group-level FDC solution, helping the customer establish an enterprise-level FDC management platform to achieve cross-fab equipment differential analysis and specification optimization.
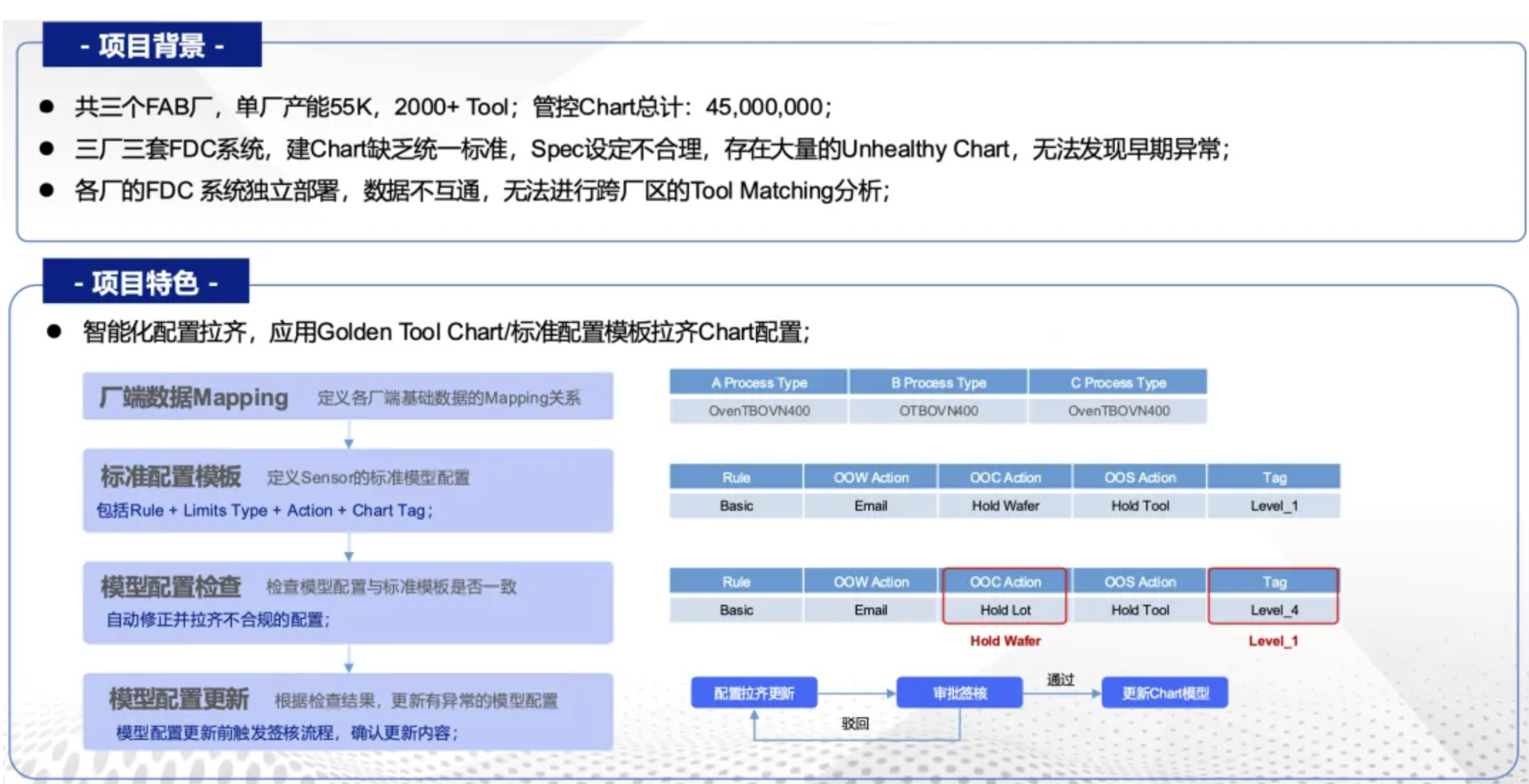
Helping customers achieve:
- Uniform Standards: Successfully established a cross-fab FDC parameter standard configuration template, achieving uniformity in the configuration of FDC systems across fabs.
- M2M Difference Analysis: Through big data analysis, identified and resolved M2M differences between multiple equipment, enhancing production consistency and stability.
- Intelligent Management: Utilized AI technology to achieve intelligent management of the FDC system, significantly improving the accuracy of fault prediction and diagnosis.
- Efficiency Improvement: Through group-level FDC data integration and analysis, generated group-level reports such as Alarm/FDC Coverage/Data Quality, significantly enhancing management efficiency.
As the first industrial intelligence solution provider in China to launch a group-level FDC solution, Gecdon's confidence stems from its over 40 years of expertise in the broader semiconductor industry, its commitment to "coming from and returning to industry," and its dedication to understanding customer needs, investing in product research and development, and consolidating solution capabilities. The semiconductor industry remains a strategic focus for Gecdon, which consistently leads in tackling challenging yet essential tasks, continuously internalizing "first principles," and starting from the essence of needs. Gecdon has tested the full-stack end-to-end services of smart factory top-level planning, solution formulation, implementation delivery, and post-operation and maintenance. To date, Gecdon has successfully assisted dozens of leading semiconductor customers in completing digital transformation across entire factories, covering different stages such as civil construction, ramp-up, and expansion, and has repeatedly been awarded the title of Excellent Partner by customers.
Looking ahead, the company will continuously iterate and upgrade its service matrix for the semiconductor manufacturing industry, focusing on AI general platform service tools and AI algorithm technological innovation based on AI and large model technologies. It will enhance core CIM systems such as MES, EAP, FDC, RMS, and QMS, AMHS solutions, and end-to-end digital upgrade services for smart factories. Gecdon will prioritize leading the popularization and application of AI in the semiconductor industry, accelerating the advancement of advanced manufacturing towards the AI era.